Before diving into the reliability program key elements, we must understand the meaning of equipment reliability.
What is Equipment Reliability?
Is the probability that an asset, item, or unit will perform its prescribed duty without failure for a given time in a specified environment.
What is the Goal of a Reliability Program?
Let’s start by exploring what is the intention of a Reliability Program. A Reliability program is designed to increase the availability and performance of the plant’s equipment by identifying potential failures and eliminating their cause or minimizing the possibility of failure and its impact.
What are the key elements for a robust program?
- Performed an Assets Criticality Assessment to identify work areas for maintenance reliability improvement actions.
- Develop a maintenance strategy based on equipment criticality- RCM, PMO or RTF.
- Assemble a multidisciplinary team to participate in the equipment reliability process.
- Institutionalize a program that engages operators with equipment reliability focus goals.
- Act on the recommendations and opportunities identified.
- Implement a system or process to capture equipment performance data.
- Establish KPI and Reports to monitor the success of the actions implemented.
Now is time to take a closer look at each key element for a reliability program.
1. Performed an Equipment Criticality Assessment
The criticality analysis provides a ranking of all equipment in a plant according to the level of importance and its probability of failure. Impact criteria to be considered are:
- Effect on Production
- Utilization
- Quality
- Safety/ Environmental
- Downtime/repair time
- Waste
- Frequency of failure
This exercise should be conducted with a facilitator that will guide a multidisciplinary team. The user (operations) and the keeper (maintenance) must participate in this exercise since they fully understand what contribution each asset makes to the organization. It is recommended to include departments that directly or indirectly have an interest in the equipment reliability such as, finance, quality, safety/environmental, among others.
One of the goals of this process is to define the functions of each asset by asking these two questions:
What its users want the asset to do?
- Primary Function- usually explain what the intention was for acquiring the asset.
- Secondary Function- what is embedded in its function such as safety, ergonomics, efficiency, compliance, etc.
Is the asset capable of doing what the users expect it to do?
This step is crucial since it creates the foundation for a well-implemented reliability program that will yield remarkable improvements in reliability and performance.
Each impact criteria should have a numeric value and a definition for each value. See the example below
Based on the numeric product/value the assets are divided into three major groups:
- Class A equipment – Most critical Assets. The target will be zero failures
- Class B equipment – Demand for maximum availability is required
- Class C equipment – Maintenance task must be kept to a minimum
2. Develop a maintenance strategy based on equipment criticality-
Numerous approaches exist to evaluate the failure modes for a system or an asset but the most common ones on the industry are:
- RCM or FMEA- Reliability Centered Maintenance or Failure Mode and Effects Analysis which evaluate the failure modes, failure effects and provide a risk priority number based on the detectability, severity, and occurrence of the failure mode/failure effects. After a risk priority number (RPN) is calculated an action are suggested to mitigate the failure mode identified.
- PM optimization- an in-depth evaluation of maintenance job plans for the asset that takes into consideration failure history and operators/mechanics experience to supplement data available.
It is essential to evaluate the benefits vs. the investment to implement the suggested actions before allocating resources to perform the reliability studies to a piece of equipment.
3. Assemble a multidisciplinary team to participate in the reliability studies
To perform a thorough reliability exercise on a system or assets we should answer these seven basics questions:
- What are the functions and associated performance standards of the asset in its present operating context?
- In what ways does it fail to fulfill its functions?
- What causes each functional failure?
- What happened when each failure occurs?
- In what way does each failure matter?
- What can be done to predict or prevent each failure?
- What should be done if a suitable proactive task cannot be found?
As you can imagine, these questions cannot be answered by the maintenance personnel on their own since some are closely related to the user intended function.
4. Institutionalize a program for operators with equipment reliability focus goals
Sometimes call autonomous maintenance or operator asset care program is an essential tool not only in preventing failures but also with the identification of opportunities for improvements. The main goal of the operator asset care program is:
- Maximize overall operating effectiveness of assets
- Build a culture of pride and ownership in the workplace
- Create a Continuous Improvement culture
- Early detection, correction, and prevention of deterioration and avoidance of failure
5. Implement the recommendations identified during the reliability studies
This is where some organizations do not follow through and do not reap the benefits of the reliability program. To see improvements, the recommendations that identified needs to be implemented. Some of the recommendations will be easy to implement and others will require a project to be implemented. I suggest you start with the “low hanging fruits” and built on top of those. A traceability matrix must be maintained to keep track of the recommendations that were implemented.
6. Implement a system or process to capture equipment performance data
Every improvement process needs a way to measure success and make decisions based on empirical data. It is a maintenance best practice to maintain the asset historical data archive for future evaluation. A Computerized Maintenance Management System (CMMS) is a tool that can help maintain records and data of the assets such as:
- Reliability studies– FMEA, Root Cause Analysis, etc.
- Maintenance work performed on the equipment
- Downtime
- Criticality Ranking/Score
7. Establish KPI and Reports to monitor the success of actions implemented
Once a system or process is established to retrieve the asset performance data a recurrent visual or numeric representation must be generated to measure the performance of the equipment and identify if the changes that were implemented are delivering the expected results. Some examples of Key Performance indicators to measure the success are:
- Mean Time Between Failures
- Downtime
- Maintenance cost per equipment
- Reactive vs Proactive maintenance
By establishing a successful Reliability program, you can achieve:
- Better maintenance cost-effectiveness
- Improvement of output, product quality, and customer service
- Longer useful life of assets
- Greater safety and environmental compliance
- An asset historical database for performance monitoring and future improvements
- Sense of ownership from operators and maintenance personnel
- Better Teamwork
Industries We Serve!
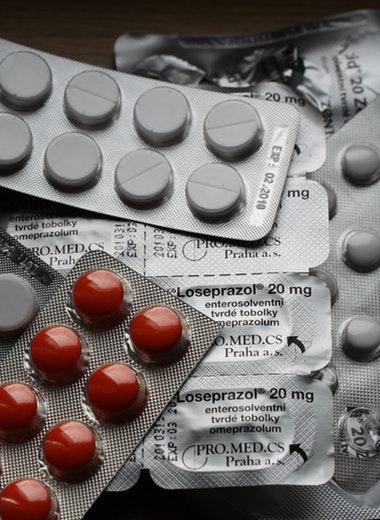
Our reliability engineers experts evaluate your plant mainteance program maturity, and develop a strategies to achieve short, middle and long terms benefits using proven world-class best practices.
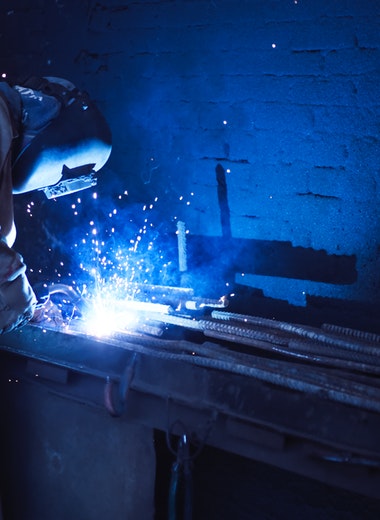
We streamline any production and manufacturing process by applying a blend of proven methodologies such as Six Sigma Lean, Overall Equipment Effectiveness (OEE) and Total Productive Maintenance (TPM).
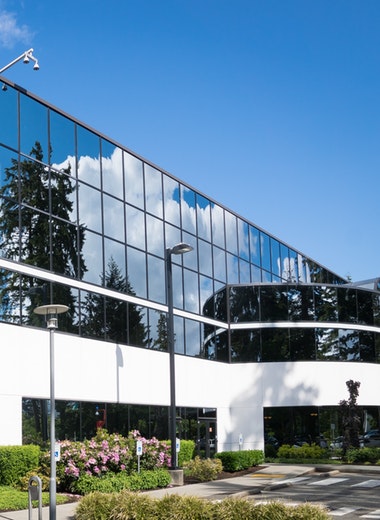
Our Facilities Services main goal is to provide operating savings by proactively maintaining the premises and supporting systems in optimal conditions. We focus on three major areas: Energy efficiency, Maintenance Cost and Equipment Reliability.